6 ways food & drink manufacturers can cut their energy costs
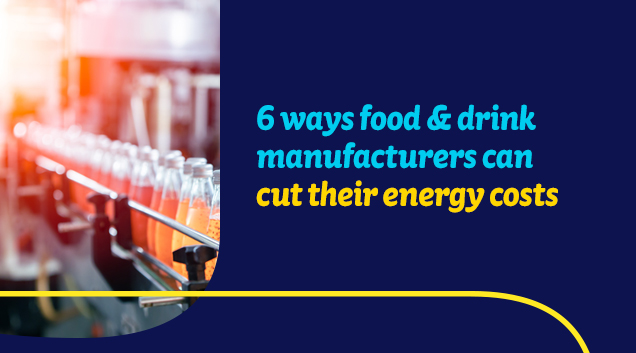
Rising energy prices have left many Food & Drink manufacturers vulnerable and exposed to market fluctuations out of their control. With energy costs accounting for an ever increasing percentage of ongoing operational expenditure for manufacturers, guaranteeing their security-of-supply to a clean, reliable source of energy is paramount.
The Food & Drink sector, like many other sectors, also faces a significant challenge to decarbonise operations. A report published by the Food & Drink Federation found that the food & drink sector was responsible for 165 million metric tonnes of carbon emissions in 2019, accounting for 17% of the UK's total carbon footprint. To meet the UK Governments commitment of net zero emissions by 2050, the food & drink manufacturing industry will have a crucial role to play in decarbonising our economy.
So how can Food & Drink manufacturers exert more control over their energy supply and reduce their carbon emissions? And what benefit does this yield in the long term on their bottom line? It is practically a given that if you can fix your operating costs, you can drive efficiencies in your production that will yield improved margins. The key question remains: how do you do this in a sustainable fashion?
A Primary means of stabilising long-term fixed energy pricing would be through onsite generation. However, this comes in many forms; and the type of generation you opt for will be heavily dependent upon the processes onsite. For example, one site might have a high electrical demand (refrigeration); another might have a high steam demand (sous-vide preparation); whilst a third might have a high heat demand (bakeries).
In all these scenarios, a solution-based approach is what is required as there is no silver bullet that will fix everything. Whether its a single technology-type, or a combination of various technologies; the correct solution can reduce a plant's requirement for energy thereby saving on energy costs as well as cutting carbon emissions.
When ABP Food Group, the UK's largest beef processor, needed an innovative energy partner to reduce energy usage and cut carbon emissions at two of its Irish plant's, we were able to provide them with a solution that will deliver a projected 66% reduction in energy usage and a projected 80% reduction in carbon emissions once all work is complete.
Energy-efficiency measures such as 1. Smart LED lighting upgrades, 2. Heat Pumps, and 3. Process Improvements (i.e. optimising energy usage through the use of an energy management hub) are measures that can be implemented that have a direct impact on carbon and cost savings.
4. Solar-PV, 5. Battery Storage, and 6. Combined Heat & Power units are the core onsite generation technologies that can help large energy users to reduce their energy demand and accelerate their transition to a low carbon future.
ESB Energy operate a £75m Decarbonisation Fund so that Large Energy users can reduce their carbon footprint while making energy cost savings. ESB Energy will build, project manage, and operated the asset for the asset's lifecycle, selling the energy or heat back to you on a long-term Power Purchase Agreement. This not only de-risks the project from a capital and O&M perspective for you; it helps to jumpstart your organisations journey to net-zero emissions without having a detrimental impact on business-critical operations.
Our range of funded and non-funded solutions make financing large-scale projects easy and affordable, while our expertise and technology ensure your organisation can dramatically reduce its energy costs and carbon emissions.
By Lebona Vernon & Michael Firth
To find out more about our partnership with ABP Food Group, read our full case study here
Let our experts jump on board with you
